Invenstory control in asset management. Who drives back home?
14 December 2012 • John de Croon
policy development, planning
Last I heard it again. ‘The inventory costs are too high. The inventory value should be reduced, but how do we determine the optimum?’ On this question we provide the answer, plus who is responsible for this.
I first took a look at some textbooks on this subject to find out what I had learned about it earlier. The formula of Camp, also known as Economic Order Quantity, can be found in literature frequently (see left)[1]. In this formula is the meaning of the elements is as follows: Q = quantity (lot size), D = annual demand of the product, F =fixed Costs, h = cost of inventory as a percentage of the price and P = price of the product.
Imagine now that a good friend of yours, a person who likes beer, unexpectedly pays a visit to you in the evening. To save costs, you had no beer on stock in your house. You could go to the supermarket by that time but if that friend has just arrived, you do not go to the store anymore. ‘If only I had ...’. What this example makes clear, is that the Economic Order Quantity does not always lead to desired results if we do not take the risk costs into account. For asset management something is missing and these are the costs caused by not having an article available on stock. Indeed, if there is a failure and the asset has no redundancy, the function may not be fulfilled a long time therefore resulting in failure costs. J.R. Tony Arnold distinguishes capital costs, storage costs and risk costs[2]. The costs caused by not having an article on stock are part of the risk costs.
In practice, the risk costs can be very low, but the value of the article can be surpassed by far as well. What to think of a turbine failure in the energy sector and there would be no spare turbine on stock, which are often difficult to obtain rapidly in the market. So it is necessary to determine the optimal inventory level based on the risks which are faced, before these inventory levels are reduced. That means that we apply the model which Ype Wijnia described in his column for the determination of inventory levels. He said that if a new kind of problem arises, you then should invent a new standard recipe for that problem. We use the Risk Based Asset Management (RBAM) process as described in ‘Asset Management for Dummies’. The inventory level belongs to the category ‘rule-based’.
For each product group we first determine what risk is faced if an item is not available. We use the risk matrix for this. There can be risks because a product is essential for the availability of a plant, but it is also possible that an article is no longer available in the market (remember the unique printer at the airport of Aruba as mentioned in the column 'Replacing an asset', resulting in an airport which could not be used by air traffic).
Is the risk acceptable, then from a risk management perspective the article does not have to be kept on stock. Of course it can be economically attractive that this article is kept on stock, for example, when the number of articles which fail is large but have little impact. Then each time when a single article has to be purchased, the costs of the purchase and the transport itself can be relatively large compared to the product price itself.
I will now briefly discuss the optimal amount. When a risk is not acceptable, then it is necessary to define mitigation measures. One possibility is to keep the articles on your own stock (option 1). A second possibility could be to have the article delivered by the supplier within a certain period (option 2). This can be formalised through a Service Level Agreement (SLA). But the supplier can also manage the inventory for you (Vendor Managed Inventory, not elaborated in this example). Suppose that your company already has a warehouse and there is no extra staff needed. The inventory costs are approximately proportional linearly (I leave out the purchase and transport costs) with the number of items held on stock[3]. The graph on the bottom left shows the inventory costs, risk costs (e.g. loss of income by a failure and the item is not available) and the total costs (= inventory costs + cost of risk). Suppose that in option 2 the supplier requires a fixed amount per annum and a percentage of the product value for the service. This then results in the cost of risk (similar to option 1) in the graph shown on the lower right.
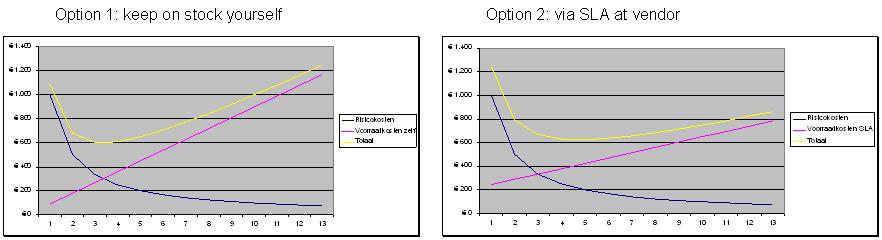
In this case, the minimum total costs of option 1 are only slightly lower than for option 2. The minimum amount for option 1 is achieved at a stock level of 3-4 articles, while for option 2 the minimum is achieved at 4-6 articles. So marginal differences in this example. Note that keeping inventory at a vendor leads to a higher inventory level than keeping it yourself does not represent reality. A sensitivity analysis and an analysis of the maximum regret (see Ype’s ‘Regret column) can help making a definitive choice.
The question that remains is who should be responsible for determining inventory levels. The Asset Manager is responsible for the balance between the operational and financial performance related to the risks which are faced. This means that the Asset Manager should therefore determine how that balance should be achieved. The Asset Manager determines the mitigation measures such as inventory levels ('the minimum amount of beer’). Then the Service Provider should be empowered to order parts if the stock level is likely to be undershot (so the Service Provider orders the beer). The operational inventory management can therefore easily be performed by the Service Provider (Service Provider holds for example the beer in stock).
This leaves only the question: who drives the friend back home. But a good Asset Manager is proactive and has obviously pre-arranged this.
[2] Introduction to materials management. J.R. Tony Arnold et all, Pearson Education
John de Croon is partner at AssetResolutions BV, a company he co-founded with Ype Wijnia. In turn, they give their vision on an aspect of asset management in a weekly column. The columns are published on the website of AssetResolutions, http://www.assetresolutions.nl/en/column
<< back to overview
|