Information helps Service Provider to be more efficient
18 May 2012 • John de Croon
program management
Due to the increasingly stringent requirements on installation integrity, reliability and availability of assets and the costs that accompany it, information is more relevant than ever. But this applies not only to the Asset Manager. The Service Provider must provide better information at ever lower costs. How this can be done and what it means for the staff is described in this column.
First, the roles must be clearly implemented[1]. Thereafter, the processes of the Service Provider can be optimised. Below is a traditional maintenance process can be seen as it is executed with various Service Providers[2].
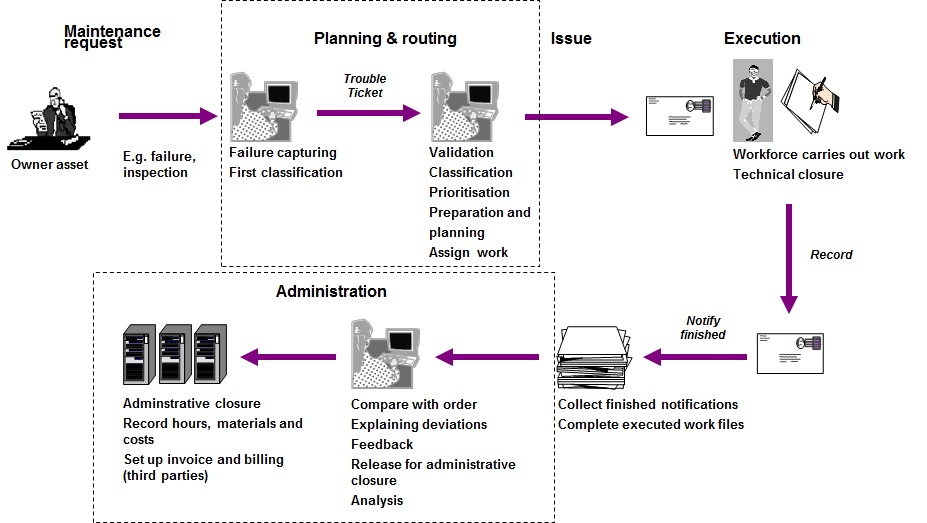
With new technologies such as mobile support, RFID (radio frequency identification) and remote monitoring of the condition of equipment cost reductions and a better system integrity can be achieved. These technologies are already used in some industries. With RFID, a system (or part of it) is provided with a chip that emits a radio signal which makes the system uniquely identifiable. With mobile support an employee works with a small computer (laptop or handheld). With remote monitoring a system is provided with one or more sensors (telemetry). These sensors provide direct (real time) or periodical (sampled) signals. From (a combination of) these signals expert systems can automatically draw conclusions, for example on the condition of the system. Think of analysis such as vibration spectra of compressors and discharge levels of high voltage equipment. Thus it can early be determined whether an asset can still fulfil its function and whether maintenance is required.
Imagine the situation where the assets are provided with RFID, every system remotely sends condition data and the maintenance technician is equipped with mobile support. The maintenance process can look like as shown below (source is again the Kluwer article).
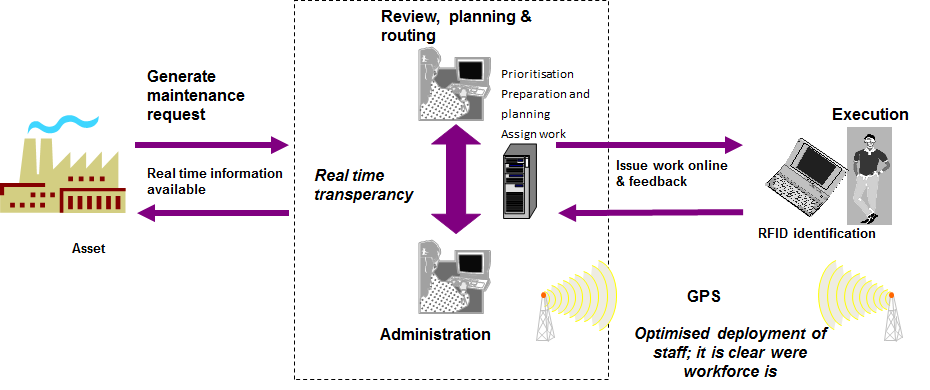
On the basis of condition data of the asset, an expert system gives the advice to execute maintenance. A planner evaluates this maintenance request, schedules the maintenance activity if necessary and assigns the work electronically. The maintenance technician has the required maintenance records digitally available. Through the RFID tag the component which requires maintenance sends a signal which is picked up by the maintenance technician’s scanner. This guarantees that the maintenance technician works on the appropriate component. With his mobile system the maintenance technician directly has access to relevant data such as the equipment location, status information (e.g. for work clearances), spare parts and work procedures. After execution of the work the maintenance technician completes the job. The used materials also have an RFID tag and are automatically recorded into the system. The maintenance technician confirms the use of these materials, fills out the time worked and enters additional inspection data. The administrative process is executed automatically and after completion of the safety procedures, the system is ready for use. The process is thus considerably more efficient and has several advantages.
The maintenance engineer has an hourly insight into the status of inspections, failures and costs. The decision script (called 'knowledge rules') from which maintenance requests are derived, is a part of the maintenance concept. This knowledge is secured for the future and prevents the Asset Manager from overflows. The role of managers will also be different. They are much less than before a 'service desk' for information and decisions to be taken. The management also receives direct insight into the performance of the maintenance processes. Due to GPS the management also knows with a accuracy of about 10 meters where the maintenance technicians are and to what risks these employees are exposed. This all sounds very nice and it is the case if it is successfully implemented. Obviously there are barriers! Maintenance technicians may feel themselves watched at and administrative functions are for example reduced.
Information technology can help the Service Provider to improve efficiency. It is the Asset Manager’s aim that the risks of the assets are managed. With modern technology it can easily be ensured that the Asset Manager is also well informed. But that is no information for the Service Provider, but for the Asset Manager. And that is already discussed in another column.
[2] See ‘Ondersteuning van onderhoudsdienst door nieuwe technologie: lastig of is het de inspanning waard?’. Maintenance Totaal, Kluwer, 2006. Peter Spaans and John de Croon (in Dutch)
John de Croon is partner at AssetResolutions BV, a company he co-founded with Ype Wijnia. In turn, they give their vision on an aspect of asset management in a weekly column. The columns are published on the website of AssetResolutions, http://www.assetresolutions.nl/en/column
<< back to overview
|